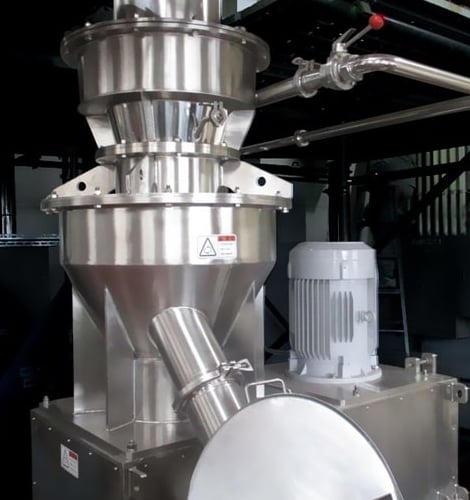
Spiral Pin Mixer Overview
- MADE FOR: Continuous mixing of dry powder or wet materials
- PERFECT FOR: Even very viscous materials
- A MASTERFUL SOLUTION FOR: Continuous dissolving and dispersion of powders and fluids as well as kneading and humidification / moistening of a wide assortment of materials
The precision mixing and processing this patented mixer is famous for is thanks to our specially designed “retention zone” which overcomes the short-path phenomenon that makes us a world apart from conventional continuous mixers.
Comes in two models, D (Dry) for dry applications and humidifying / moistening and W (wet) for dissolving and kneading applications.
What makes PME's Spiral Pin Mixers Special?
The Spiral Pin Mixer is extremely effective on even highly viscous materials (up to 10s of thousands of cP) and can dissolve and homogenize as well as knead and cake those materials.
The Spiral Pin Mixer can process a large volume of material with a small, compact footprint.
Compared to other mixers the Spiral Pin Mixer is easy to maintain and the rotor is easy to remove.
It’s easy to clean and takes fewer manhours to maintain.
The rotor pins are in a spiral formation helping ensure uniform processing regardless of the course the materials flow.
We offer optional extra coatings to prevent wear and contamination.
Heating and cooling jackets are also available.
Fewer clogs, less sticking.
Clogs and materials sticking to the machine are both issues that cost you time, money, and keep you from getting the consistent high-quality output your enterprise needs. We devised this special method to avoid blockages and keep materials from the sticking to the surface that usually occurs when liquids and powdered material come into contact and create a viscous sticky mass.

Feeding
Powder and liquid materials are fed into the mixer from separate pipes. The liquid material passes through the feed pipe and forms a thin layer from the gap between the lower part of the dispersion rotor which rotates at high speed and the upper part of the mixing rotor and is diffused to the outer periphery.
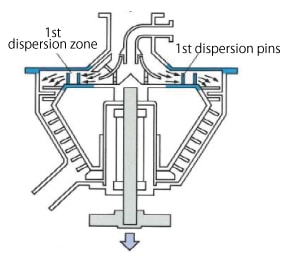
First Dispersion
After being fed into the mixer the liquid and powder are first joined on the upper surface of the mixing rotor.
At this stage the mixture is then sheared by the primary dispersing pins which are arranged in a spiral on the top of the mixing rotor which rotates at the extremely high speed of 15 m/s producing a strong shearing force dispersing the mixture roughly to the outer periphery.
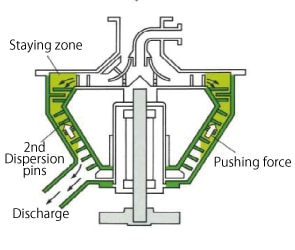
Retention Zone
WHERE THE "MAGIC" HAPPENS: After the joining and initial shearing in stage 2, we still don’t have the level of mixing needed for many current applications of mixed materials.
The mixture created in the previous stage now enters the downward slope from the upper outer periphery.
As the mixture is now rotating in a vortex, the centrifugal force of the material itself keeps the mixture pushed up creating a 'retention zone' with the upper end of the discharge port as the boundary.
The mixture remains in this staying zone sequentially for about 7 to 12 seconds during which it is subjected to severe shearing force by the secondary dispersing pins. After sufficient mixing and dispersion are repeatedly performed the mixture is then discharged in a highly sheared state.
[Advantage of Retention Zone]
Conventional continuous mixers have a weakness; they undermix materials and have issues with producing uniform output and dispersion.
- The Spiral Pin Mixer corrects this issue using the retention zone to remix and shear with a high shearing force for a set amount of time so we can prevent lumps, homogenize even highly viscous materials, and even fluidize / liquify solids such as dewatered cakes.
- This graph shows elapsed time on the x axis and the throughput (kg/min) of the input and output of powder material on the y axis. The consistency of the output material has a very small variance even though the viscosity of the materials is significantly different.
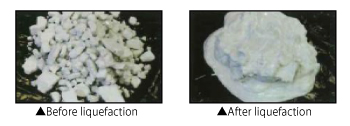
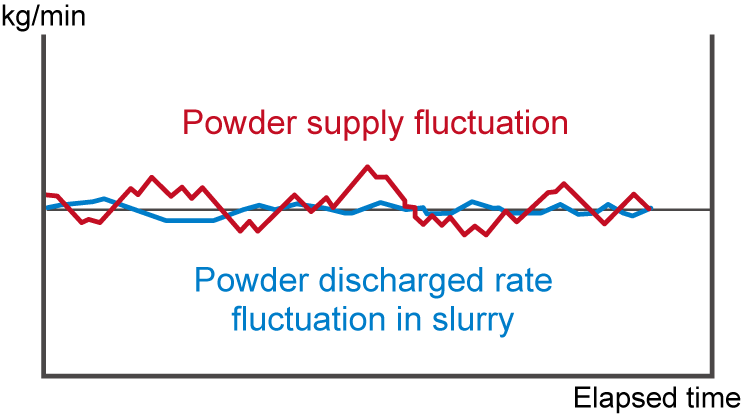
The Spiral Pin Mixer is used for mixing up to 100,000 mPas. See reference chart below to see what that means in liquids of various viscosities.
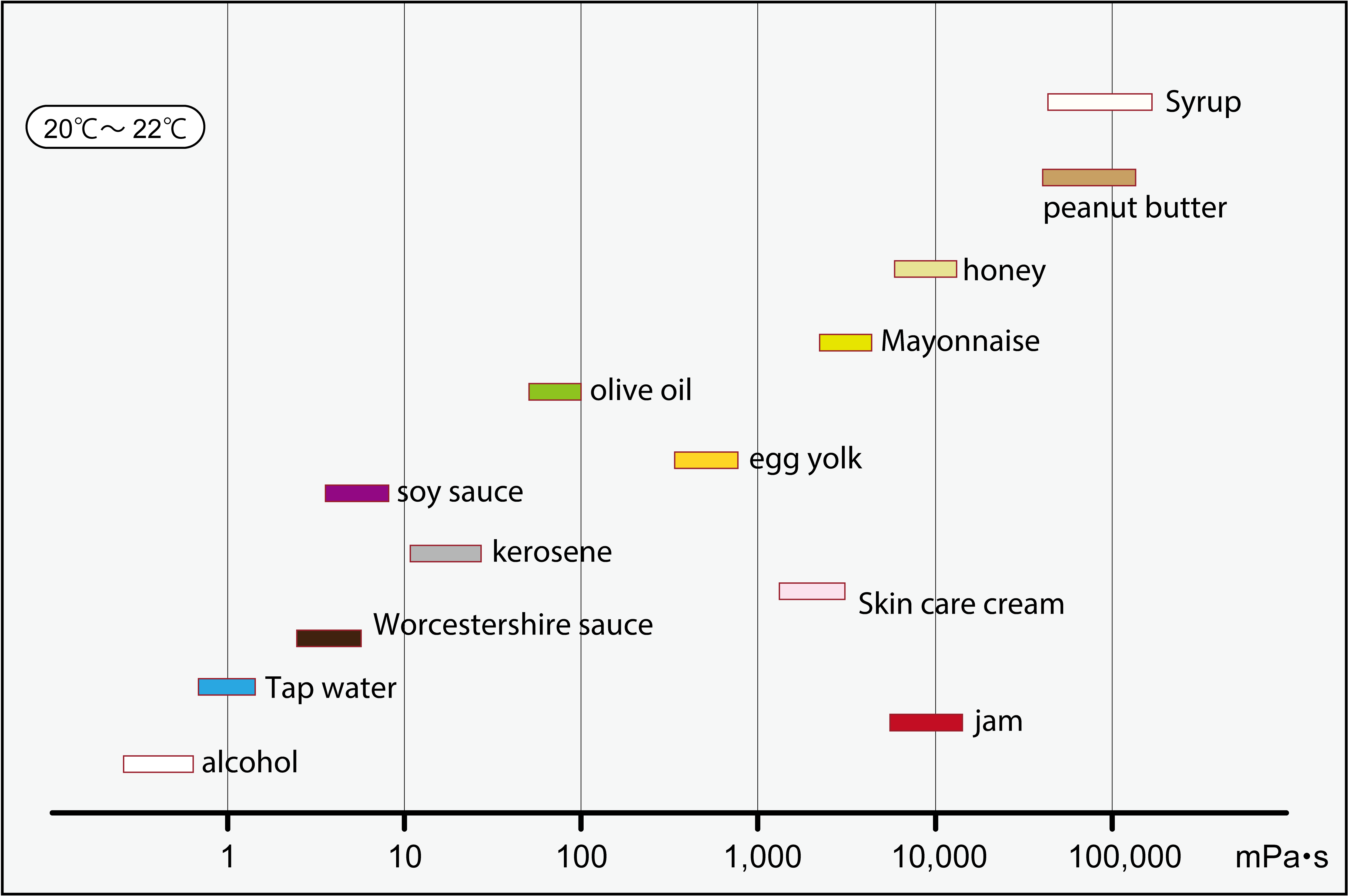
Continuous vs. Batch processing; the continuous processing advantage
Greater output, smaller plant footprint saves space & increases output.
As an example, say the Spiral Pin Mixer processed 6000 liters of output in 60 minutes. If the same company used their batch processor to achieve the same output volume in the same time span, they’d need between 2 to 20 batch mixers instead of just one PME Continuous Pin Mixer.
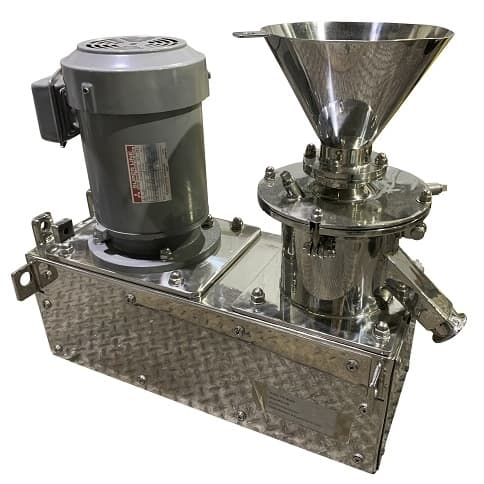
Spiral Pin Mixers
PME Spiral Pin Mixer's Approximate Processing Volume
To process the following volume: 6m3・H(6000L/H):
Equipment |
Volume |
Processing Volume |
Processing Time |
Required Equipment |
---|---|---|---|---|
Spiral Pin Mixer | SPM-55W (6000L/H) | 6000L | 60 minutes | 1 mixer |
Tank + Propeller mixer | Effective capacity 100L tank(1 tank, 20 minutes to produce one batch of output) | 6000L | 60 minutes | 20 tank + mixer combos |
Tank + Propeller mixer | Effective capacity 500L tank(1 tank, 20 minutes to produce one batch of output) | 6000L | 60 minutes | 4 tank + mixer combos |
Tank + Propeller mixer | Effective capacity 1000L tank(1 tank, 20 minutes to produce one batch of output) | 6000L | 60 minutes | 2 tank + mixer combos |
The Spiral Pin Mixer outperforms other mixing methods and takes up far less space all while delivering a very high standard of output product.
*Schematic diagram of SPM-55 type attached, please refer only to general dimensions, other models have a different design but similar size / footprint.
Simple, elegant design.
The entire mixer cleans easily with just a little cleaning fluid thanks to the self-cleaning design.
Maintenance is simple and quick because the top cover and mixing rotor can be easily disassembled.
And because the liquid and powder are fed in through separate systems there’s little adhesion and blockage of the entry port.
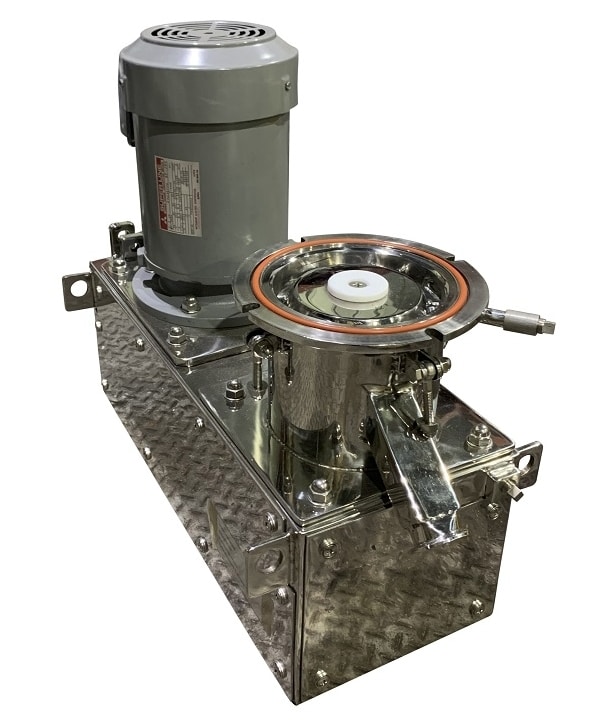
PME Spiral Pin Mixer Models
We carry two base models, the W (Wet) or D (Dry)
Specifications by Model
W Series Mixers for Wet Dissolution / Mixing
- Required powder and capacity are based on the dissolution process (about 1000CP)
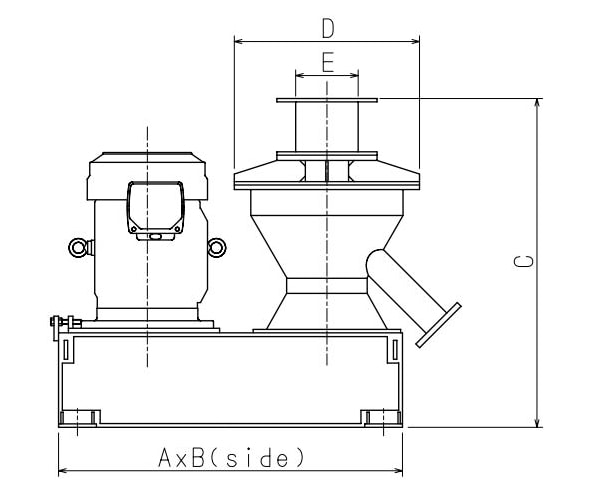
Model |
Performance (liter/Hr) |
Motor (kW) |
Dimensions (mm/inch) |
Weight
|
||||
---|---|---|---|---|---|---|---|---|
A |
B(Side) |
C |
D |
E |
||||
SPM-15W | 250 | 1.5 | 560/22.0 | 220/8.7 | 440/17.3 | 210/8.3 | 50A/2 | 150/331 |
SPM-25W | 1,000 | 2.2 | 695/27.4 | 300/11.8 | 570/22.4 | 300/11.8 | 80A/3 | 200/442 |
SPM-40W | 3,000 | 5.5 | 910/35.8 | 400/15.7 | 841/33.1 | 480/18.9 | 100A/4 | 300/662 |
SPM-55W | 6,000 | 11 | 1,150/45.2 | 550/21.7 | 1,131/48.5 | 640/25.2 | 150A/6 | 600/1,325 |
SPM-70W | 12,000 | 18.5 | 1,400/55.1 | 700/27.6 | 1,403/55.2 | 820/32.3 | 200A/8 | 1,000/2,208 |
SPM-85W | 20,000 | 30 | 1,650/65.0 | 850/33.5 | 1,624/63.9 | 1,000/39.4 | 300A/12 | 1,300/2,870 |
SPM-100W | 30,000 | 45 | 1,940/76.4 | 1,000/39.4 | 1,901/74.8 | 1,180/46.5 | 400A/16 | 1,650/3,642 |
SPM-115W | 40,000 | 55 | 2,300/90.6 | 1,150/45.3 | 2,178/85.7 | 1,360/53.5 | 50A/20 | 2,200/4,857 |
SPM-130W | 50,000 | 75 | 2,620/103.1 | 1,300/51.2 | 2,453/96.6 | 1,510/59.4 | 600A/24 | 2,700/5,960 |
D Series Mixers for Dry Mixing / Humidification
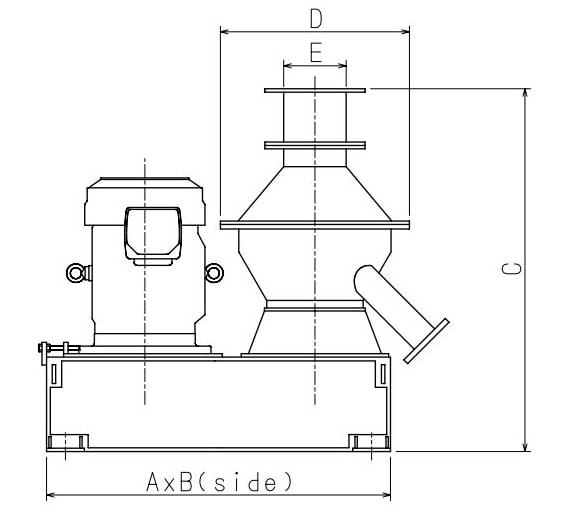
Model |
Performance (liter/Hr) |
Motor (kW) |
Dimensions (mm/inch) |
Weight
|
||||
---|---|---|---|---|---|---|---|---|
A |
B (Side) |
C |
D |
E |
||||
SPM-15D | 300 | 2.2 | 560/22.0 | 220/8.7 | 480/18.9 | 210/8.3 | 65A/2.5 | 160/353 |
SPM-25D | 1,000 | 3.7 | 695/27.4 | 300/11.8 | 650/25.6 | 330/13.0 | 80A/3 | 220/486 |
SPM-40D | 3,000 | 7.5 | 910/35.8 | 400/15.7 | 960/37.8 | 510/20.1 | 125A/5 | 350/773 |
SPM-55D | 5,000 | 15 | 1,150/45.2 | 550/21.7 | 1,230/48.4 | 670/26.4 | 200A/8 | 650/1,435 |
SPM-70D | 7,000 | 22 | 1,400/55.1 | 700/27.6 | 1,450/57.1 | 850/33.5 | 250A/10 | 1,100/2,428 |
SPM-85D | 10,000 | 30 | 1,650/65.0 | 850/33.5 | 1,680/66.1 | 1,010/39.8 | 350A/14 | 1,450/3,201 |
SPM-100D | 15,000 | 45 | 1,940/76.4 | 1,000/39.4 | 1,950/76.8 | 1,220/48.0 | 400A/16 | 1,800/3,974 |
SPM-115D | 20,000 | 75 | 2,300/90.6 | 1,150/45.3 | 2,200/86.6 | 1,400/55.1 | 1,500A/20 | 2,500/5,519 |
SPM-130D | 30,000 | 90 | 2,620/103.1 | 1,300/51.2 | 2,450/96.5 | 1,560/61.4 | 600A/24 | 3,000/5,623 |
Materials : Carbon Steel, 304/316/316L Stainless Steel
Wear resistant treatments: Hard Facing / Stellite Spray / Ceramic Pins
INDUSTRIES AND APPLICATIONS
Battery Components
Homogeneous dispersion of active materials into binder solutions is the key to better batteries. Mixing, heating, drying, catalytic reaction mixing battery pastes is a specialty.
Chemical Industry
Mixing of powders, humidification, lump dissolution.
Pigments / Paints
Fluidization of pigment cakes. Mixing of paint and synthetic resin.
Resin
Mixing of resin powder. Mixing of liquid resin, feeler, solvent, additive, powders. Dissolution and mixing of silicone oil.
Food
Humidification and mixing of powder, liquids and fats. Production of base liquids, dissolution of thickeners. Mixing of slurry before spraying and freeze-drying.
Cosmetics / Detergents
Formulation of base liquids such as creams and emulsions. Mixing of paste-like substances such as toothpaste. Oil humidification and slurry formulation for powder detergent.
Pharmaceutical
Mixing, humidification, and dissolution of raw materials. Mixing of ointments, etc.
Ceramics / Mining
Mixing and humidification for powders of lime and talc, Ceramic slurry mixing (before spray drying). Dissolution of tile raw material.
Electrical / Machinery
Mixing of magnetic paints, insulating materials, etc. Mixing and humidifying battery raw materials.
Fuel
Mixing of COM (Coal-Oil Mixture) and CWM (Coal Water Mixture). Pre-mixing of emulsion fuel.
Paper / Textiles
Dispersion of neutralizer. Mixing of bleach paste, clay solvents.
Civil Construction
Mud shield, cement slurry for tunnel backing, mortar mixing. Mixing of soil improvement agents. Mixing of cement slurry for injecting into seabed
Building Materials
Mixing of light weight concretes. Dissolution and mixing of panel and board raw materials.
Fertilizer / Pesticide / Feed
Humidification, mixing, and dissolution of raw materials.
Water / Sewage / Wastewater
Dispersion and dissolution of polymer flocculants. Dissolution and fluidization of dehydrated cake. Mixing of incineration ash before humidification and solidification.